Whale MFN
EOM Offshore - Summer 2019
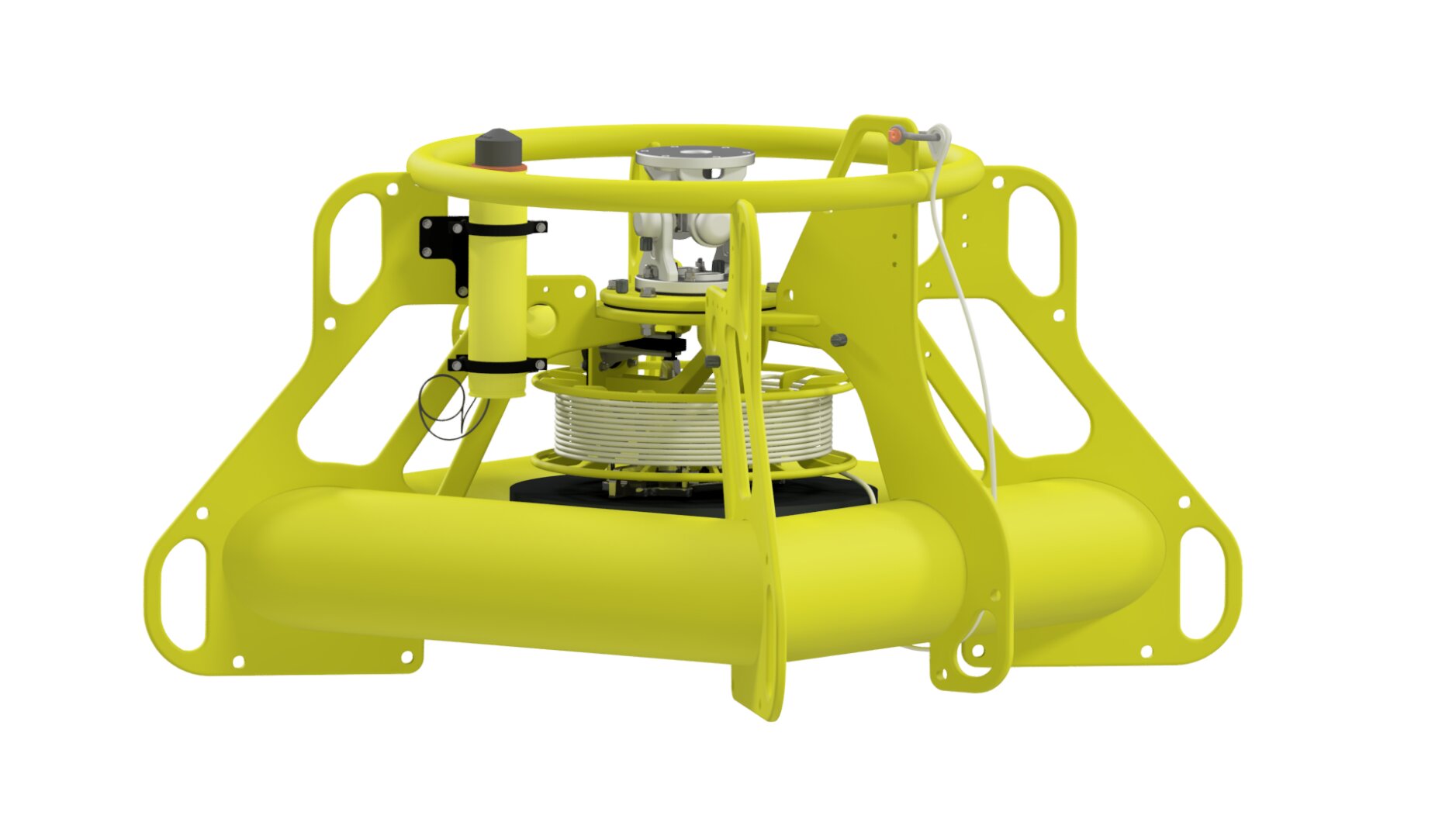
As my first project while interning at EOM Offshore, I was responsible for the conversion from 2D drawings to 3D models of the Whale Multi-Function Node (MFN), designed to serve as a recoverable anchor for buoys. The project involved creating models of 45 parts, as well as combining them into their weldments and assemblies. After a rapid completion of the drafting portion of this project, I also supplemented the models with an animation of the operation of the MFN. All these tasks were completed using Autodesk Inventor.
As a second phase to the project, I was asked to optimize the design to reduce cost and complexity. To accomplish this, I modified various parts to remove the need for 5th axis CNC machining and waterjet cutting, allowing all parts to be manufactured on a 3 axis CNC router. In order to reduce material cost, I used Inventor’s Stress Analysis environment to optimize the design of each part, concluding in dramatically reduced material usage from the original design.
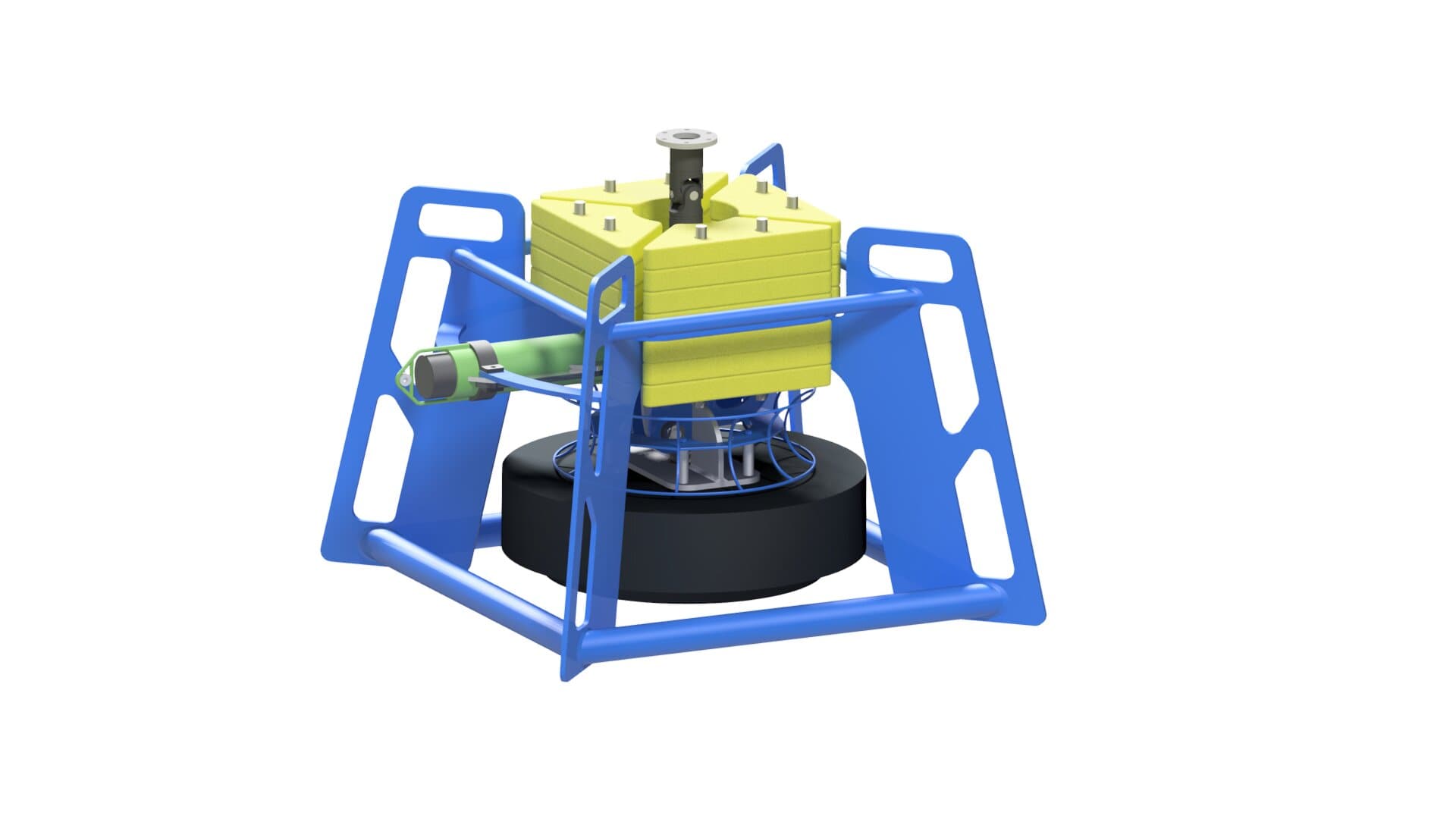
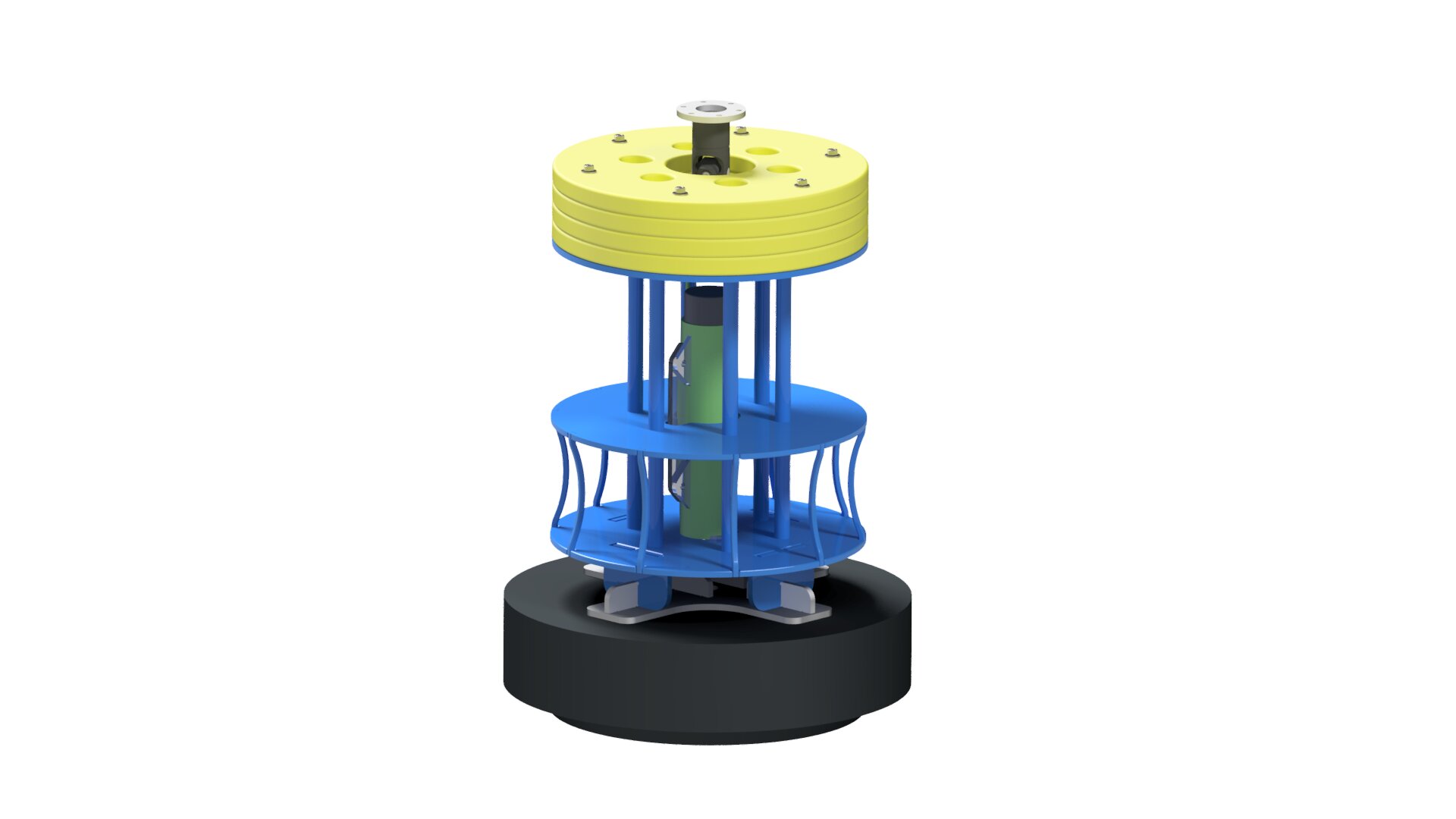
While working on the optimized design, I found inspiration for a new form factor for the MFN, that further reduced machining cost, cutting material use nearly in half from even the optimized design, while allowing for the same functionality offered by the original design. I accomplished this mainly by redesigning the complex anchor release system to be replaced by a single part.
Unfortunately, my return to school prevented me from being able to fully test and validate either new design, and the company ended up manufacturing the original node design. To complete the project, I wrote extensive assembly documentation for this design, including detailed renders completed in Inventor’s Studio environment.
As a part of this project, I used and developed my skills in engineering design and optimization, Autodesk Inventor, finite element analysis, product rendering, and use of the Microsoft Office Suite.
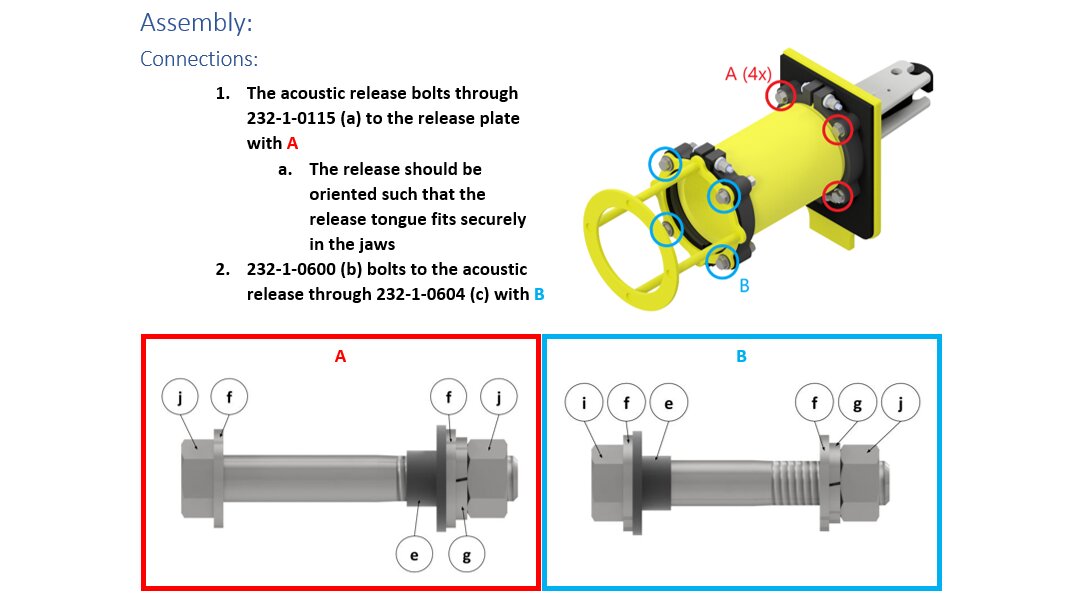